Finished Project
Our completed vehicle successfully held the weight of two riders, was fully faired, and ran under the power of a spring steel belt drive system connected to sprag pulleys on a central drive axle. We were able to compete with the vehicle at competition under the power of the belts for several miles, and learned many valuable lessons along the way. Since we ended up with so little time between the completion of our vehicle and when we had to leave for competition, the events in Indianapolis served as testing for our proof of concept. Below are excerpts from our daily log of competition:
Day One:
We worked inside the hotel to get our drive system back up and running, got our spring system refined and added important last minute requirements like seat belts and a rear wheel cover. Moving the Orka backwards...not so good! It over tensions the system and threatened to blow our pulleys. We took a spare sprag welded to a sprocket and used it as our new idler. This was definitely a last minute modification, but it did allow the sprag to lock and grab the chain before the belts took catastrophic loading. Riders were instructed to "Avoid reverse at all costs."
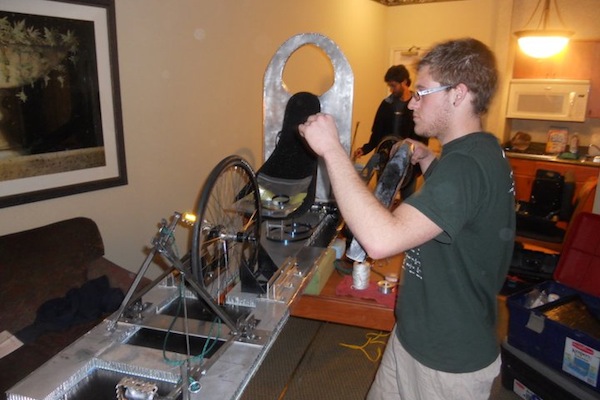
Day Two:
We headed to the Speedway for our safety checks, visual inspection, and questioning about our vehicle modifications. We did quite well and the judges were impressed with our system. Taping sharp edges on the belts near our legs, a few long bolts were trimmed, and taping the carbon edges of our fairing were the only safety changes required by judging. The entire group was called to a separate staging area for a photo session with all crafts and teams on the Brickyard straightaway! The photo session ended and we proceeded back to safety where we completed the turning and braking tests. It was decided that steering was a bit shakey, so we used the portable flux core welder supplied by a team mate to add some steel on the steering tabs. This was a dramatic improvement on our steering.
Unfortunately we were not able to shift with our drive system. We had some difficulty in getting our entire belt system running front to back, so we did not have time to add the additional shifting linkage. However, we found that running in top gear was possible by using short, fast strokes of the pedals to start and then working into longer more powerful strokes as we gained speed. The belt rollers inside the shifting sliders that are on the vehicle are in need of more modification after discovering more friction than we had originally anticipated in that part of the system.
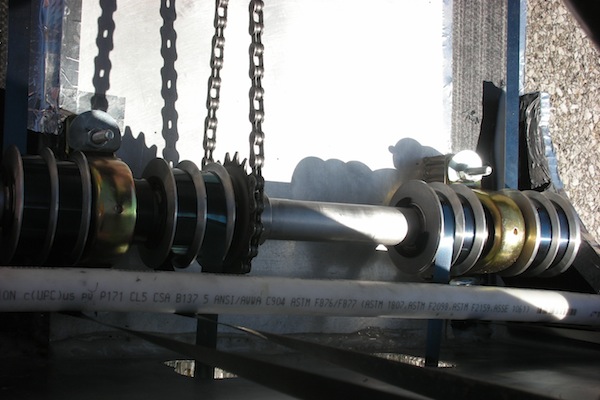
Day Three:
The sprint competition was the first day we were able to put our entire fabric fairing onto the bike and see our entire creation in the light. It's pretty cool, and the comments were amazing throughout the entire competition. "Work that whale" and "Free Willy!" were shouted at us frequently. The goal of the men's sprint was to qualify us for the open round where we could try for better times. The vehicle started off fast, but the chain fell off in the speed trap and the "scooter" approach was used to get an average speed of 4.5 mph. The slider pulleys gave us more trouble and we were forced to hit pit row again to fix the rollers. Our women took the vehicle back on the track and we got a time trap speed of 9.5 mph. (SLOW, but heavy friction could be heard giving the craft a notable "Orca noise... is that why it's called the orca?"). We again took the rollers off and replaced them with PVC to see if sliding over smooth plastic would help. We got back in line and were told that the sprint open call had closed. We were not granted acceptance to another sprint run.
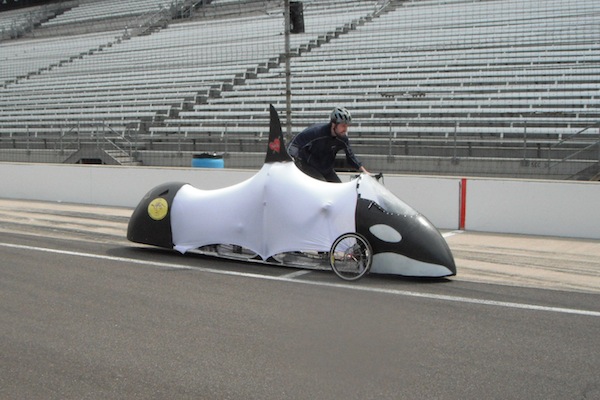
Day Four:
We re-analyzed the PVC rollers and determined that it was the best system we could come up with for the endurance race. We moved the pedals closer to the seats at rider request and welded them together in order to reduce torsional deflection at the pedal mounts. Steering was checked again and our other systems were checked for damage. We got the vehicle into the lineup and determined that the rain and fog on track would inhibit rider visibility inside the fairing, so the fabric and rear cover were not used. (Speeds were also slow and full aerodynamic capabilities versus rider visibility came to an obvious decision).
Our ladies team (Rachael and Marilla) started the first three laps and FINISHED ALL THREE ON BELT DRIVE POWER! The chain fell off once due to idler misalignment but that was a fast fix. The girls came through smiling and the crowd was wild for the Orka.
We swapped in our male lead team (Erik and Kyle) to power down and a belt snapped in the pits on both the front and rear drive. Due to the friction and variations in slider pulleys, the belts had fatigued near the levers and broke under the stress of professional cyclists' brawn. Instead of changing the entire belt, we un-wound one or two of the safety winds from the drive sprag pulleys and re-clamped the belts. The men took off again but a very considerable friction gain was apparent. The belts again failed and in the next pit inspection we found that the PVC rollers had ceased to roll and had instead worn/melted a small groove into the pulleys! We did get a good lap time, however, by leaving the front rider on-board and having the rear rider stand on back to push the craft along. We successfully created the most advanced, expensive skateboard in human powered history. After our second and third belt failure, there was not time to completely re-build the drive system AND make new roller pulleys. The lever pins were tapped out of the bearing rests, belts were un-clamped and the whole pedal assembly was removed to save weight and make room for our riders to "scoot" the bike along. We actually managed to PASS other teams with this method (Good thing we got our new wheels the day we left! Again, Chris King hubs held up to their shining reputation as the best bearings in the cycling industry). Riders were impressed by the incredibly smooth rolling motion of the bike and effortless pushing. All rider teams were able to complete the minimum three laps and several did even more. In all, we completed (3+3+4+4+2) 16 Laps! GO NAU.
The awards ceremony had great food and an interesting outcome. We were hoping to get some sort of design award (5th due to ???, we will review judgement papers upon their release) and thought we might get the ingenuity or team spirit award, but to no avail. We DID tie for 1st in the "aesthetics" category but because it was tied into design, we did not get any recognition for it. A separate award was created for us to recognize our never-before-seen drive system and we got an Indianapolis Motor Speedway puzzle that was deemed the "WHALE OF A DESIGN" award. We were hoping for some higher-ranked prized, but at least when we stood to receive our award, the entire crowd clapped harder than ever. That was good enough!
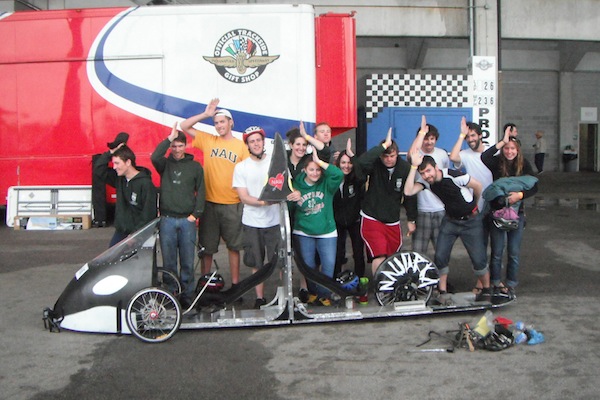
In conclusion, we were pleased with the success of our vehicle and learned many valuable design lessons from the project. Our drive system was incredibly complicated and never before implemented on a human powered vehicle, so some difficulties were expected. The fact that we were able to complete several miles of track under the power of the belt drive proves that the system does work. The struggles we dealt with showed us that there is plenty of room for improvement and that this vehicle does have true potential to a real competitor in the future.