Design Cycle
The following is information on the design cycle process used by the HPVC capstone team. It includes our milestones, tools used for design, our development process, testing, and problems we encountered.
Significant Milestones
HPVC Milestones include the following deliverables that were created by the team and agreed upon by the team and Capstone professor. Each of these deliverables were assigned a due date and the team was expected to submit appropriate information or physical representations to fulfill each.
Deliverable #1: CAD Drawings for Fabrication, due February 1, 2011
The team was tasked with generating CAD drawings from the vehicle model in Solidworks to help with the fabrication of custom parts. All drawings needed to be dimensioned and presented clearly and logically so each part could be replicated by anyone with machining skills and without additional instruction other than what was given on the drawing.
We successfully completed this deliverable by the set deadline.
Deliverable #2: Drive Shaft "Works Like" Prototype, March 1, 2011
The team chose to create a "works like" prototype of the unique drive system that will be used on the Human Powered Vehicle. The prototype was to be created to give the team a definitive idea of the feasibility of the one-way sprag bearing drive and return system. If the prototype were to yield unsatisfactory results, the team would return to the original belt drive concept and implement that on the vehicle as a part of the final design.
We successfully completed this deliverable by the set deadline and determined that drive system would be feasible. From there, we decided to continue forward with our final design of the sprag bearing drive and return system for implementation on the final vehicle. A photo of our "works like" prototype is shown below. The prototype was fabricated from balsa wood, dental floss, pins, and wood glue.
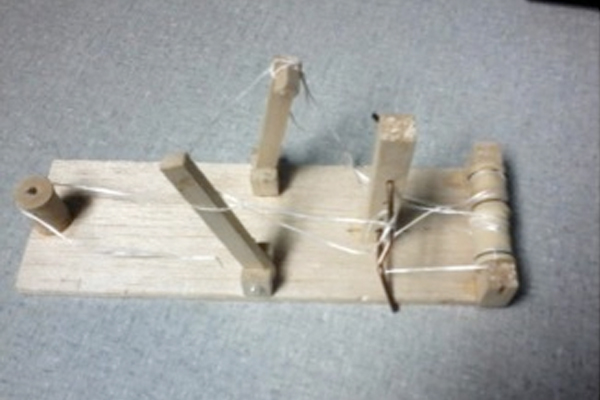
Deliverable #3: Rolling Chassis, March 26, 2011
The team decided to have a rolling chassis by March 26th. However, due to parts and materials on back-order and significant design changes to the vehicle frame, the due date was changed to April 2, 2011.
The rolling chassis was to consist of all three wheels mounted to the vehicle frame with the necessary components. The vehicle should roll and maintain structural integrity under the weight of two people.
We were able to have a rolling chassis by April 2, 2011. We fabricated the front and rear wheel mounts and successfully attached them to the frame. However, by the due date of this deliverable, the frame had been epoxied for only 48 hours and had not finished curing. Since this was the case, we did not feel confident in putting the frame under the weight of two riders. Also, our rear wheel and hub was still on back-order, so we temporarily mounted a spare wheel to the vehicle and did not permanently attach it due to varying dimensions in the spare hub and hub on order. A photo of the rolling chassis is shown below.
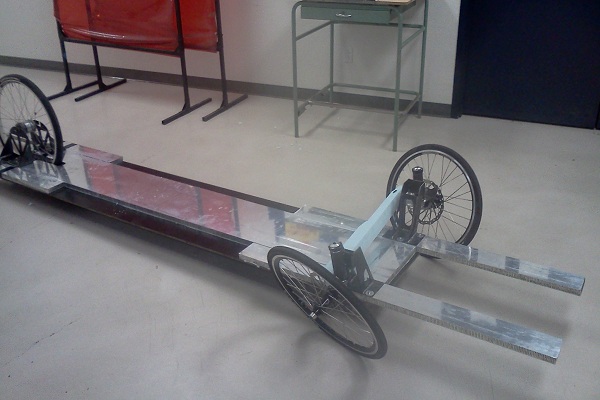
Deliverable #4: Completed Vehicle, April 12, 2011
The team originally chose to have a completed vehicle by April 12. However, due to the date move of Deliverable #3 and parts still on back-order, the team has requested a date change for April 25, 2011. At this time, the date change is still pending approval.
The completed vehicle will be a finished frame with all components installed and properly working, as well as a fairing. The completed vehicle will be used for further rider training and testing, and will then be raced at the 2011 HPVC East event in Indianapolis, Indiana.
We are currently working hard toward this final deliverable and have a partially completed vehicle.
Tools Used for Design
Solidworks CAD software has been key in the design process for the HPVC. All initial concepts and the final vehicle design have been modeled with Solidworks. By having all parts created in this program, the team can access any part or assembly within the vehicle and take dimensions for fabrication. Solidworks is also used to take these parts and export them to Cosmos for analysis. With Cosmos the team has been able to analyze the deflection of critical vehicle components, such as the frame and wheel mounts.
Development Process
The HPVC design evolved from concept to prototype to final design through testing. The initial concept that was chosen had been researched prior to selection. The research was influenced by previous experience and testing with similar materials for the vehicle frame and components.
The prototypes used for the HPVC were a test of feasibility. The drive system prototype proved to the team that the system would work, and also shed light on the aspects of the design that needed more work. As modifications were made, they were tested with additional prototypes and CAD models.
The final materials that were chosen for the vehicle, especially the honeycomb and epoxy used for the HPVC frame, were tested for strength and deflection under the weight of two riders. These tests let the team to know that the carbon graphite and Nomex core honeycomb panel would not be strong enough on its own, and would require the additional support of aluminum honeycomb strips. The epoxy used to hold the honeycomb panels together was also tested to ensure that the roll cage would remain upright and not tear away from the frame in the event of an accident.
Problems Encountered
This project has brought the team together to overcome several complications, especially in the design and fabrication phases. The team has had a difficult time obtaining materials and parts, and due to these unforeseen struggles, there have been several redesigns.
One of the first problems encountered was finding a honeycomb panel that would work for the vehicle frame. The team originally wanted to use titanium honeycomb, but the companies that manufacture that particular type of honeycomb were unable to provide the team with the requested material. The final honeycomb that the team was given to work with was very different from the titanium honeycomb that was originally figured into the design, which prompted a redesign of the frame and new analyses.
A second problem encountered was the drive system. The team originally designed for a belt driven drive system with lean steering, but later met David Calley, founder of Motor Excellence, who proposed a new type of drive system using steel belts and pedal levers. Since the design was not finalized, it continued to evolve in the coming weeks and remained in the design phase until late in the overall fabrication of the vehicle. It took a massive effort to finalize the design for the drive system and implement it on the vehicle effectively, and is still undergoing small design changes as the concept becomes a reality. Since the new drive system required so much effort to design and implement it, the team chose to not use lean steering to reduce weight and complexity and made the appropriate design changes to support a fixed steering system. Another problem was obtaining parts and materials. Many of the components needed to complete the vehicle were ordered with no issue and then later reported to be on back order. Those parts, including the wheel sets, created a serious delay in the ability to have a rolling chassis or completed vehicle at their original due dates. Should the parts not come in before the team leaves for competition, parts will be taken from the previous year's vehicle and adapted to meet the needs of this year's bike.
Lastly, one of the biggest problems encountered with the design and fabrication of the HPVC was time. No matter how much planning and scheduling was done, the team was always running on a set of tight deadlines. It was difficult for the team members to balance the demands of school and this project simultaneously, but perseverance and dedication enabled us to complete a lot of work in the short amount of time we had.