State-of-the-Art Research
Advanced Materials and Composites
In an attempt to find a unique material to fabricate the vehicle frame from, the team researched several options, including titanium honeycomb and carbon composite. Titanium honeycomb is difficult to obtain, but unique for the application of a vehicle frame. The honeycomb is extremely lightweight and has a high strength-to-weight ratio. The honeycomb is also relatively easy to work with – it comes in sheets, it is easy to cut, and easy to attach components to.
The team has contacted and is currently working with Benecor, Inc™, a titanium honeycomb manufacturer for the aerospace industry, to determine more about the cost of the material and possible donations.
Another material option the team considered for the vehicle frame was carbon fiber composite. Carbon fiber is also lightweight and has a high strength-to-weight ratio. However, many teams at the HPVC competitions already use carbon fiber on their vehicle for frames and fairings, which means this material does not carry the "unique" aspect our team wants to achieve. Carbon fiber is also difficult and time consuming to work with, requiring lay-up molds and autoclaving to achieve optimal performance parameters. At this time, Northern Arizona University does not have the facilities to support work on large-scale composite fabrication. Our team would need to sub-contract with local companies such as NovaKinetics, LLC™ or Quintus, Inc™ to obtain materials, workspace, fabrication facilities, and composites expertise.
Components
A variety of high-end bicycle components from different manufacturers have been recorded to a database for reference. High quality components are quite expensive, but their quality and durability is generally much greater than lower priced options. Since our vehicle will contain two riders, it will receive twice the "wear-and-tear" during each race event at competition, our team requires the most robust and lightweight components that we can afford.
The components currently chosen for the vehicle include cranksets fitted for belt drive instead of conventional chain drive, an independent drive system specifically for tandem bicycles, internally geared hubs, custom fabricated recumbent seats, and simultaneously activating dual disk brakes for three wheeled bicycles.
Belt Drive
Rather than connecting the drive system of the vehicle with heavy metal chains as in a traditional bicycle, belt drive systems are under consideration. Belt drive systems are lighter than traditional chain-drive systems, easy to work with, low maintenance, and last twice as long as a conventional bicycle chain. These aspects will help the team achieve the goal of creating a unique, ultra-lightweight vehicle.
Gates Carbon Drive Systems™ manufactures polyurethane and carbon fiber belt drives for bicycles. The team is currently in contact with a representative from the company who is helping to acquire belts and drive systems for our vehicle. Figure 1 shows a mock-up of the belt drive system the team is planning to use. This graphic, along with a document detailing our needs, was sent to Gates Carbon Drive Systems™.
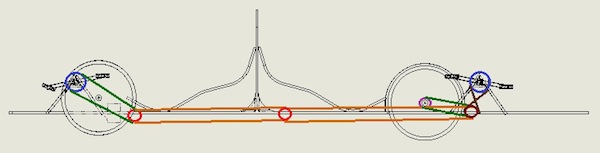
FIgure 1. Belt Drive Layout
Lean Steering
After attending the 2010 HPVC West competition, members of the team were interested in learning more about lean steering, which was featured on some of the vehicles at the 2010 competition. Lean steering incorporates a linkage system that allows the wheels to actually lean with the vehicle when making turns. This helps reduce wear on the tires and allows riders to lean into turns rather than just turning a set of handlebars or maneuvering a steering joystick. Lean steering also reduces the lateral load on the wheels created by centrifugal forces, therefore keeping the wheels from buckling during high-speed maneuvers. Figures 2 and 3 show two similar lean steering concepts the team has created based on our research.
Figure 2. Lean Steering Linkage, Concept #1
Figure 3. Lean Steering Linkage, Concept #2
Wheel Sizes and Gearing
The wheels sizes were chosen carefully because efficiency and performance had to be considered. A large wheel has a smaller rolling resistance, but experiences higher stresses in tight turns, while a smaller wheel will have smaller aerodynamic drag at high speeds and will allow for quicker acceleration.
Consequently, we have selected 20-inch wheels for the front of the vehicle and a 24-inch wheel for the rear. The rear drive wheel must be larger than the front wheels because it will allow for more flexibility with gear ratios. Our gear and wheel ratios must work out so that the riders will be pedaling at an optimum cadence of about 80-90 revolutions per minute at a 45 mile per hour speed.
Rider Ergonomics and Efficiencies
The team researched various rider positions and associated efficiencies for pedaling bicycles. It has been found that the most efficient stance for a rider is the recumbent position with the bicycle seat at a 37° incline. This is a compromise between an aerobic endurance position and an anaerobic sprint position. It is important that the rider be in an appropriate position to maintain proper blood flow though the legs and feet. To allow for maximum power output and optimum muscle recovery, the seat will be placed on sliders so that each rider can adjust their position for peak efficiency. The maximum pedal distance will need to be 110% of the distance from the rider's hip to heel. This will reduce the angles created at the hops and knees, which will reduce the moment forces experienced at those joints. This allows for longer recovery periods between pedal strokes and less stress on the muscles and joints. Detailed measurements of the appropriate rider stance are shown in Figure 4.
The average person operates at about 23% efficiency, which means that a cyclist trying to achieve a speed of 45 miles per hour will need to output 350-400 watts of energy. If 23% of the total energy is used for propulsion, the rider will generate 1000-1200 watts of heat. To keep the rider from overheating in an enclosed fairing, a method of cooling must be applied. The human body needs to stay within ±2° Fahrenheit of the core temperature (98.6° Fahrenheit) to maintain a high power output. Air ducts, fans, and aluminum seats with ventilation are being taken into consideration for proper rider cooling.
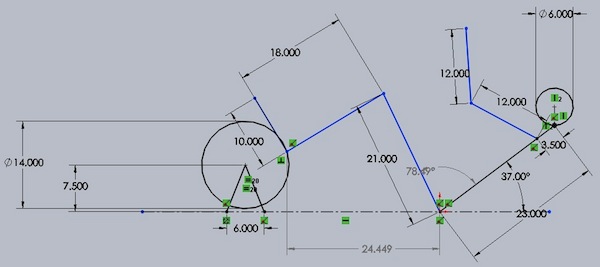
Figure 4. Recumbent Rider Position