|
PROTOTYPE FABRICATION |
|
|
|
|
|
Envelope |
|
|
The envelope was based on
outer dimensions specified by Raytheon including bolt spacing for
mounting to other optical components. The actual part was Computer
Numerical Control (CNC) machined from 6061-T6 Aluminum by
R&D Specialty
Manco located in Phoenix, Arizona to a tolerance of +/-0.005
inches. The actual envelope is seen in Figure 1.0 below. |
|
|
|
|
|
Figure 1.0 - CNC Machined Envelope |
|
|
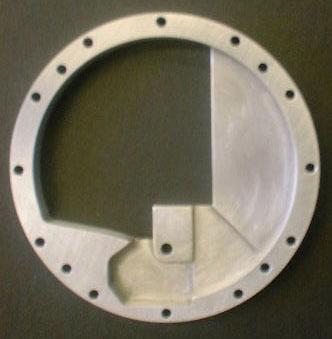 |
|
|
|
|
|
positioning Arm |
|
|
The outer dimensions of
the positioning arm were machined by the Northern Arizona University
machine shop from 7075-T6 Aluminum due to its higher ultimate tensile
strength to a tolerance of +/-0.01 inches on width dimensions and
+/-0.002 inches in thickness. The germanium lens frame was later CNC
machined by the members of the team to dimensions specified by
Raytheon. See Figure 1.1 below to see the positioning arm in
production and Figure1.2 of the positioning arm with a Laser Sintered
prototype of the germanium lens inserted into the lens frame. |
|
|
|
|
|
Figure 1.1 - Positioning Arm During Machining of the Lens Frame
|
|
|
Figure 1.2 - Final Arm With Prototype Lens |
|
|
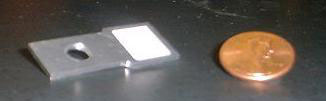 |
|
|
|
|
|
bushing & pin |
|
|
The bushing was fabricated
on a lathe from Oilite Bronze by K&M Machine in Flagstaff to a
tolerance of +/-0.001 inches. The pin was machined from 4041 Heat
Treated Steel. Both pieces can be seen below in Figure 1.3. |
|
|
|
|
|
Figure 1.3 - Oilite Bushing and Steel Pin |
|
|
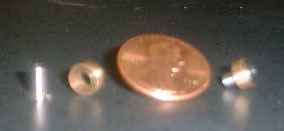 |
|
|
|
|
|
Completed prototype |
|
|
The fully assembled
prototype can be seen below in Figure 1.4. This prototype will be
provided to Raytheon for possible dynamic testing in a Rail Gun Test. |
|
|
|
|
|
Figure 1.4 - Completed Prototype |
|
|
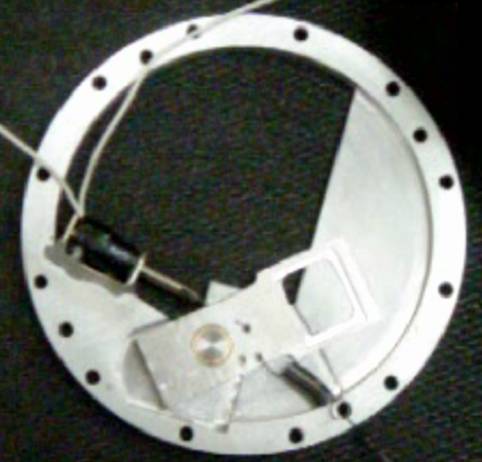 |
|
|
Click Here or on picture
above to play a clip of the mechanism |
|
|
|
|
|
|
|