Design Decisions
Initially, we planned on using a damping material to minimize the vibration on the battery pack. When we looked into the vibration effects on batteries, it was found that, simply tightly securing the pack limits the vibration. Since the batteries will be on a road trailer with suspension, any vibration caused by the road surface would be greatly reduced by the suspension.
The initial design for the support members was to use 2”x1/4” strip steel. This could handle axial loading but when a bending analysis was performed, it was apparent that there needed to be a greater moment of inertia to resist bending forces. This is when the C-channel was chosen. After a fatigue in bending analysis was performed, using the mod Goodman failure criteria (1), it was found that a 3"x1.41x4.1 C-Channel will be adequate. The weakest member (weakest orientation of member) had a factor of safety of 1.2, which meets our specifications.

In order to attach the battery holder to the underside of the trailer, there needed to be a way to accomplish that. The first idea was to just weld the support members directly to the trailer’s I-beams. Since this would make removing the mounting system after it was installed very difficult, the support members would be welded to a steel plate and then bolted to the I-beams using the existing brackets used to hold the diesel tank. In order to ensure that the welds will be adequate, a fatigue analysis was performed using the Gerber and Langer failure criteria (2). It was found that there needed to be more weld area on two of the members to meet the specification. To accomplish this, ribs were added (shown below). This gave a final factor of safety of 2.47 for the weakest weld.

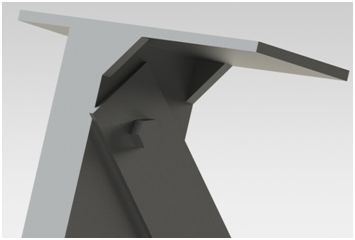
The mount system was then taken to Professor Alarick Reiboldt for suggestions. He suggested that diagonal members be added, to make the mount structure be more like a truss. This makes the structure resist against twisting and adds support to the main supporting members.
The design for the strap that holds the battery pack in place requires only one bolt. Since we wanted the pack to be easily removed from one side we came up with a track that the one side of the strap could easily slide in and then bolt the other side.
Final Design
The design for mounting the battery pack to the underside of the trailer uses a basic truss design. This design was chosen because it protects against any unforeseen forces caused by the road roughness, without adding a significant amount of weight. Each support is specified to hold the entire load of the battery pack. This creates a built in factor of safety of 4.
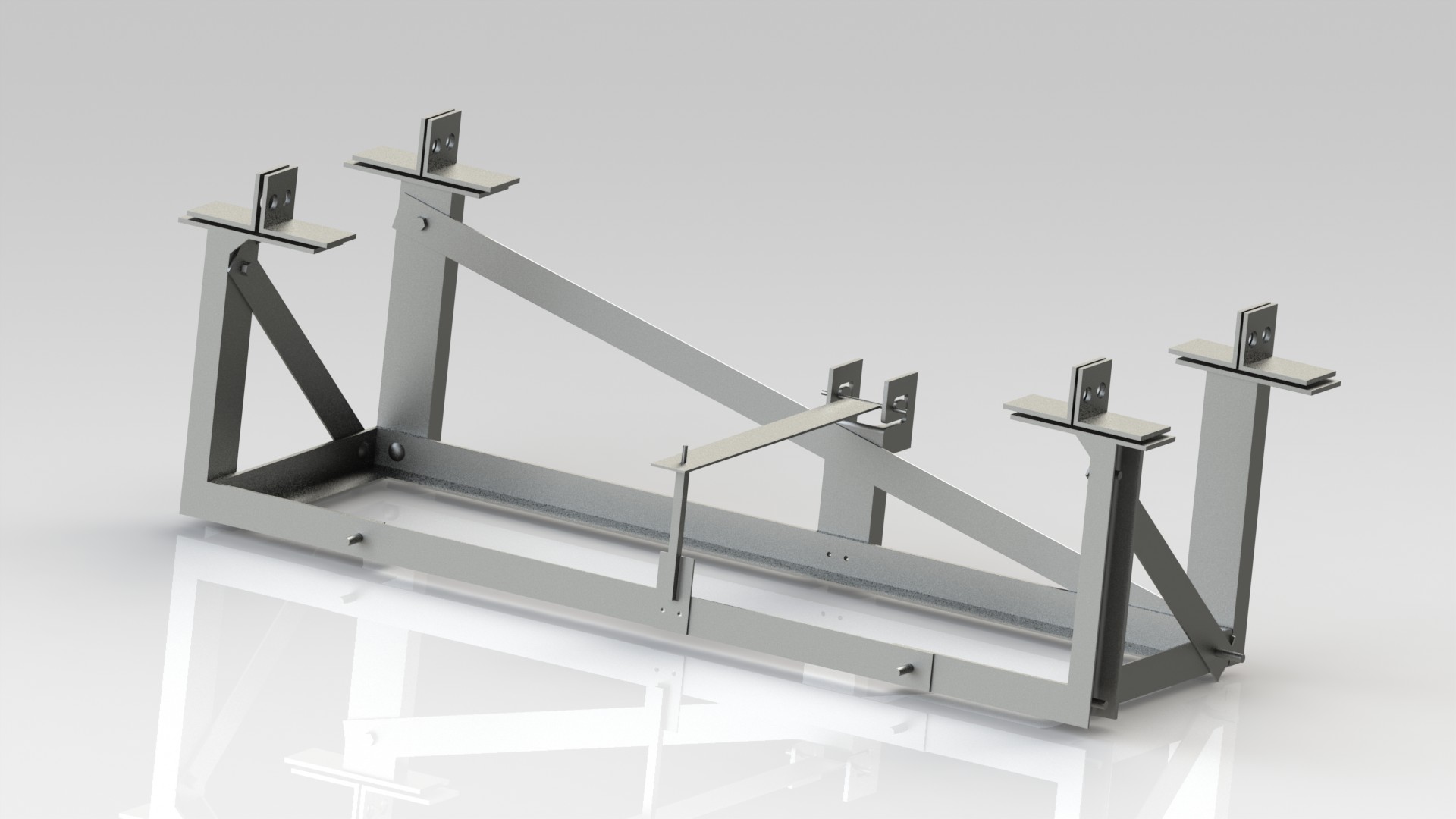