STM Tips
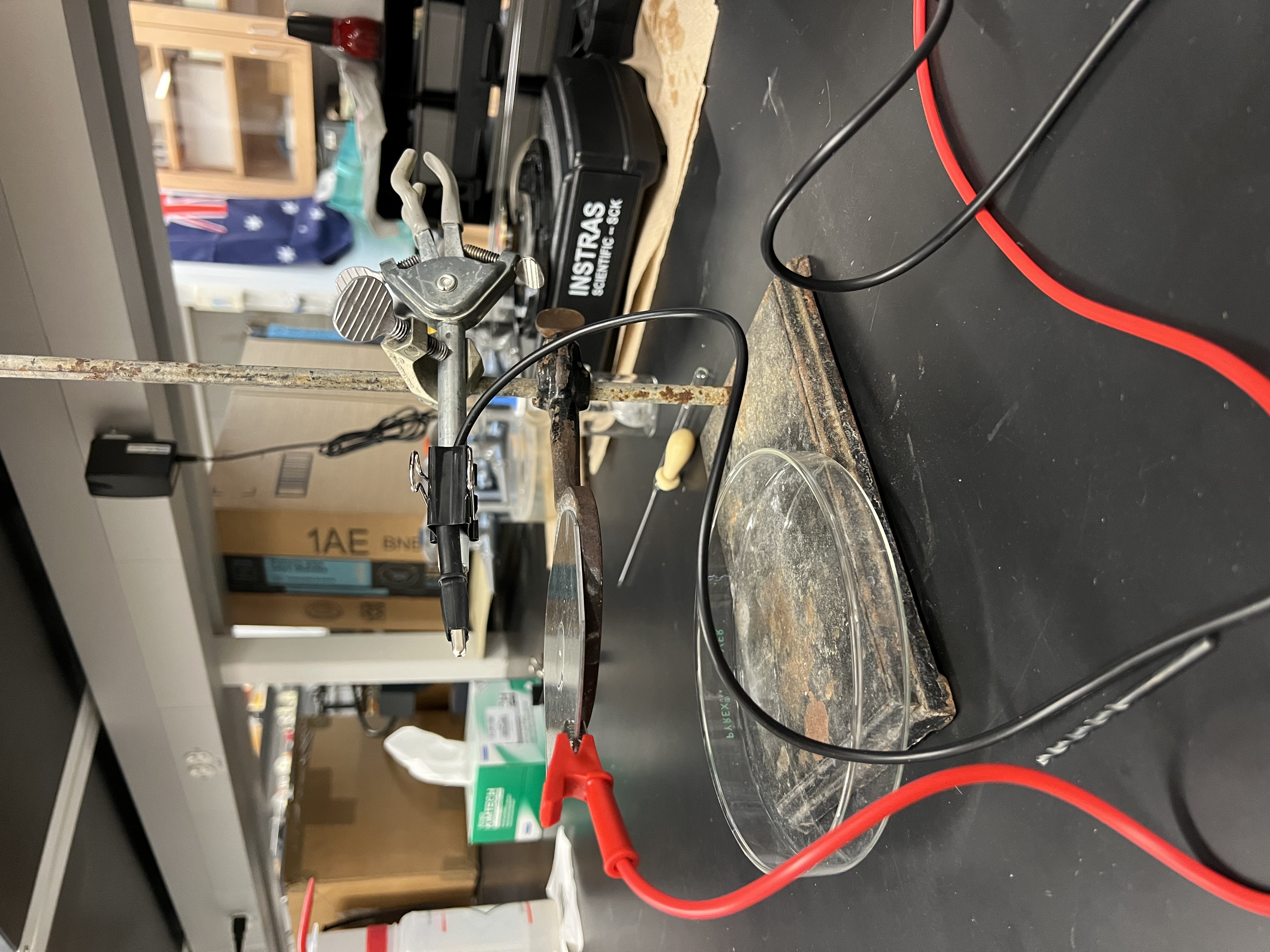
Etching Process

an etched wire imaged using a scanning electron microscope
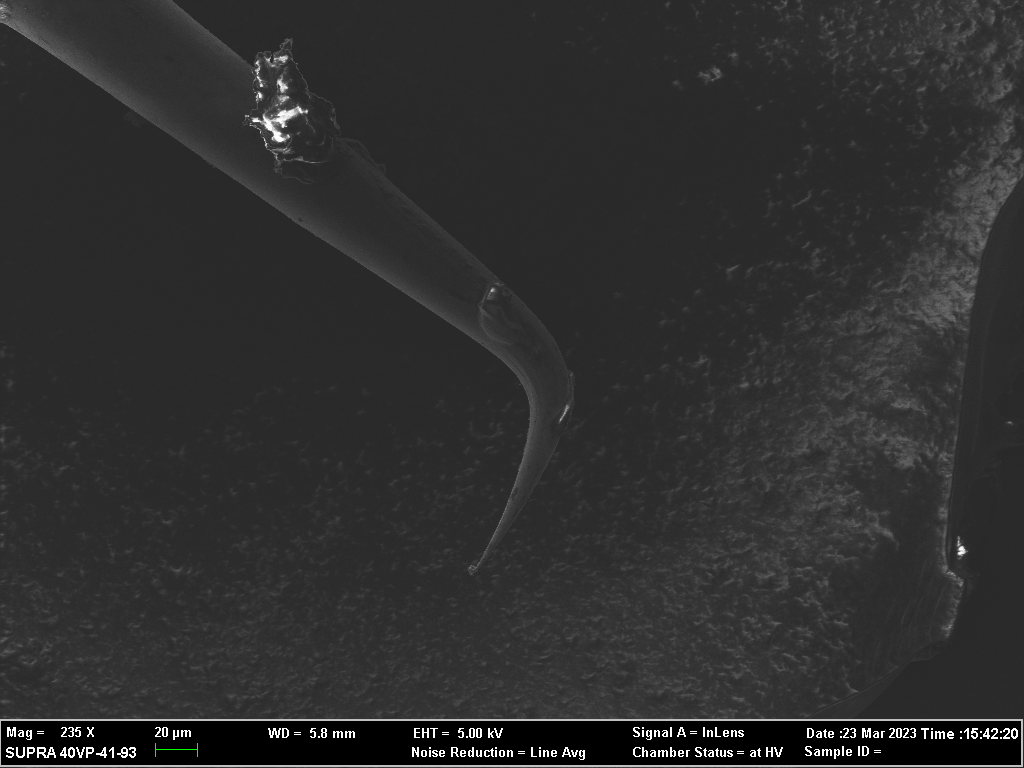
an example of a bottom half tip with a bent end with tungsten deposits on it
The scanning tips are made of tungsten that is electrochemically etched using Potassium Hydroxide(KOH).Â
Tungsten was used due to its strength--to make the tip more resilient to tip crashes--and the fact that it does not oxidize in the open air at room temperature, thus keeping the scanning tip as sharp as possibleÂ
The tungsten wire is fed through and held in a hole in a stainless steel plate and a Petrei dish filled with shaving foam is placed underneath to receive the bottom half of the wire when the etching is complete. The hole in the stainless steel plate is then filled with KOH and approximately 9 volts is applied between the plate and the wire(the negative terminal is connected to the wire).Â
With this setup, the etching lasts for about 1 minute and produces two tips--one from the top half and one from the bottom half.Â
This process still needs to be improved, though, as the bottom tip was bent to the side in several batches and both sides had tungsten deposits on and around the tip that was likely caused by the KOH solution getting over-saturated with tungsten.Â
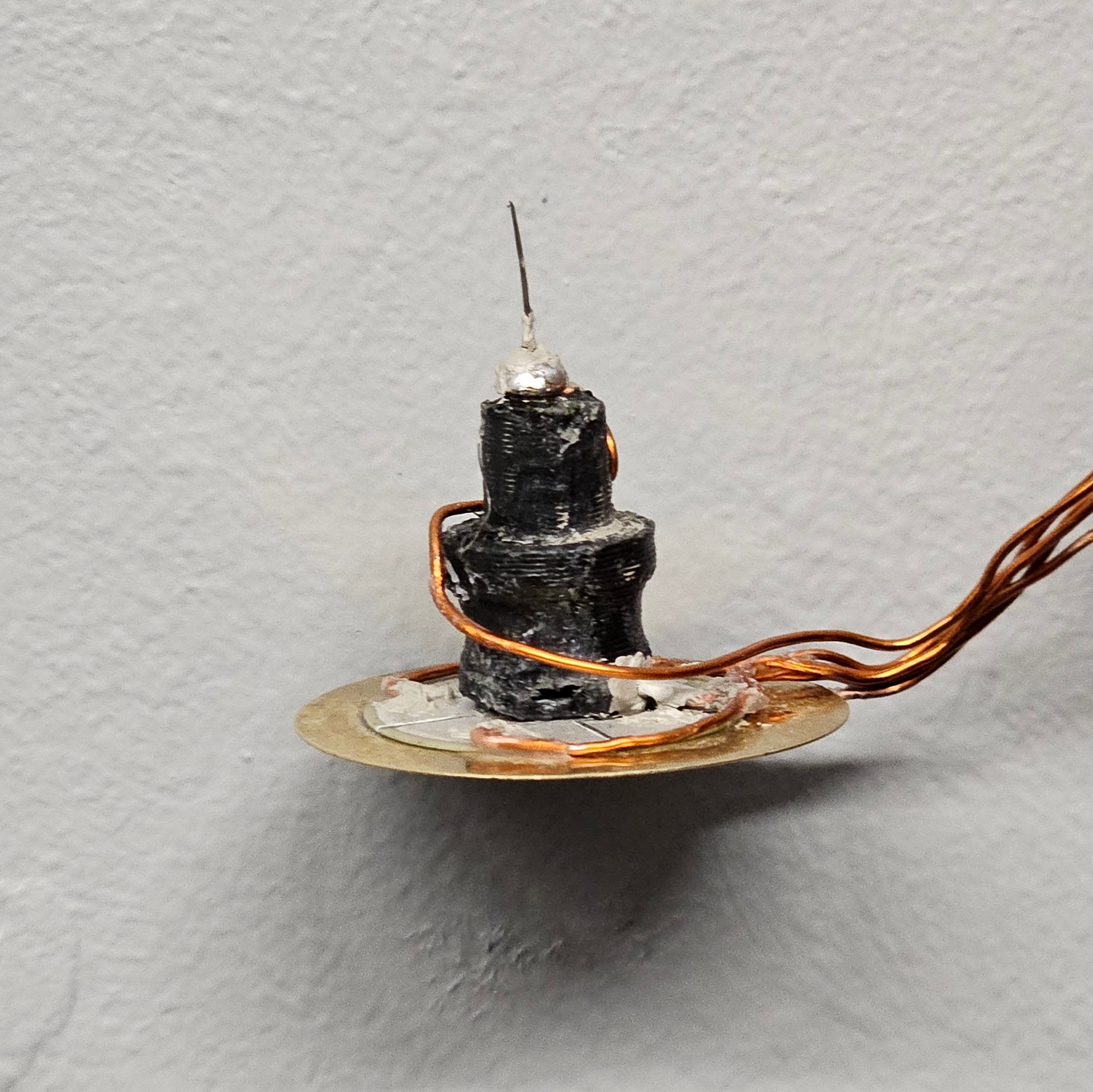
After the tip is etched, the tip wire is shortened and inserted into a male-to-female header pin that is inserted into a 3D-printed post attached to the piezo buzzer. The header is then filled with silver paste to form an electrical contact between the header and the wire; this allows for a separate wire to be easily connected from the tip wire to the preamplifier.Â