The Project
Abstract
Dual axis solar tracking arrays increase overall efficiency by positioning photovoltaic panels incident to the sun. These arrays must be large and heavy in order to withstand inclement weather, making them bulky and expensive. Creating an "intelligent array" capable of responding to harsh weather conditions would allow smaller lightweight installations capable of the same power output while minimizing cost. This array would respond to wind loading, snow loading, and collision detection. Overall power output is also improved utilizing a backtracking algorithm whereby panel-to-panel shadowing is eliminated. The presence of partial shadowing on a panel causes a dramatic decrease in power generation, predominantly observed during sunrise and sunset. A dual axis solar array will demonstrate "intelligent array" capabilities while being controlled autonomously by a programmable logic controller (PLC).The PLC code used to control the array will be written, tested, and debugged during this project.
Problem Statement
Solar panel arrays are a new emerging technology with constraints which prevent it from becoming more commonplace for personal use. Despite a recent breakthrough in photovoltaic technologies, overall efficiencies are still low; through a new tracking technology overall efficiency can be increased, so that for the same arrays more energy can be harvested. A two axis solar tracking system can gain an additional 40 % power production when compared to a stationary array that is installed correctly, as seen in Figure 1.
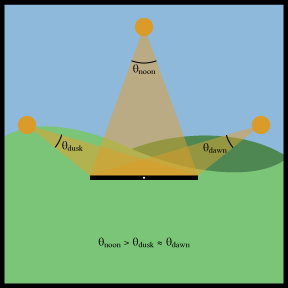
(a) A fixed-panel installation
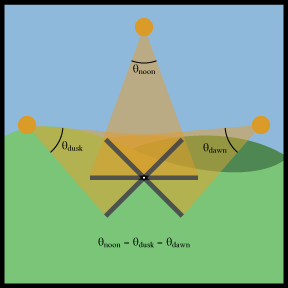
(b) A sun-tracking installation
Figure 1: Comparison between fixed and tracking instalations
A second deterrent to personal solar arrays is the cost of installation to protect against strong wind (wind loading). Existing technologies require large concrete footers as well as reinforced steel piping to withstand wind loading, (Figure 2a). The solution to wind loading would be to create a smart system capable of detecting and responding to high winds. Parking or stowing solar panels in a louvered position during high winds would allow for lighter, less expensive installations (Figure 2b). This savings in cost would in turn lead to a faster return on investment for a personal solar array.
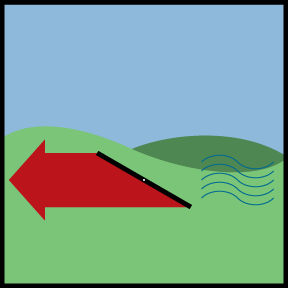
(a) A tilted panel experiencing heavy wind load
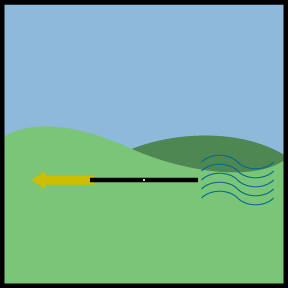
(b) A parked panel minimizing wind load
Figure 2: Explaination of wind loading and preventative parking
A third obstacle to a two axis solar tracking system is self-shading, a situation in which adjacent panels block the sunlight from each other and which causes a drastic reduction in power production (Figure 3a). A properly designed intelligent tracking array would also be capable of detecting and avoiding self-shading based on the dimensions and spacing of the panels as well as their angle when tracking the sun (Figure 3b).
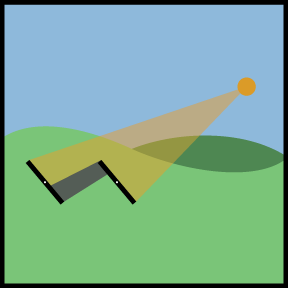
(a) A self-shadowing array
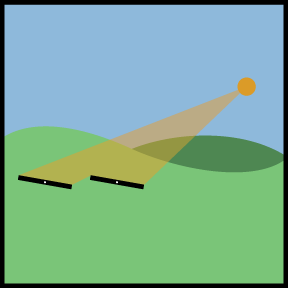
(b) A backtracked (and unshadowed) array
Figure 3: Description of self-shadowing and backtracking
System Diagram
A block diagram of the proposed system is seen below in Figure 4.
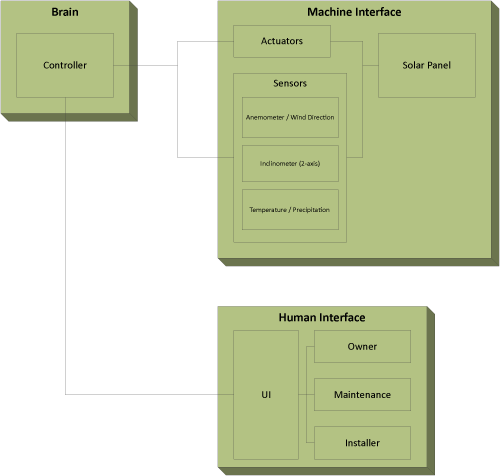
Figure 4: Proposed system block diagram
Requirements
Marketing requirements have been established to better appeal to the consumer. These requirements fit into the following categories: mechanical, electrical, environmental, testing, documentation, and general.
Mechanical Requirements
Mechanical requirements were established to increase the robustness and ease of use. The system's components must be small enough to mount on the solar tracking frame, and also be protected from the elements. In addition, standard interconnects between the controller and all sensors must be standardized and weatherproof. The system must be organized for easy maintenance. The weight and size of the panels dictates the type of actuators chosen. The system must be able to control these actuators.
- Less than 5 ft³ and under 40 lbs
Electrical Requirements
The widest possible tracking range must be accomplished to track the sun from horizon to horizon. The system's electrical components and peripherals must also be robust enough to function beyond the point of return on investment.
- For 99 % accuracy, ±5°
- Operate for 10 years (twice the Return On Investment period)
Environmental Requirements
Environmental factors must be considered to ensure the reliability of the system under harsh conditions. All components must be protected from the elements, and resistant to any related vibration or shock encountered during turbulent weather. All components in said system require industrial temperature ratings.
- Wind-driven rainfall (NEMA–4)
- Industrial temperature range (−20 °C–70 °C)
- Survive winds of up to 40 mph in tracking position
Documentation Requirements
In order to maintain the procedures and knowledge regarding the installation and upkeep of the system, detailed documentation will be required. Any and all coding used in the project will be amply annotated. The platform on which the code is written will depend of course on the programmable logic controller and its associated software. In addition, an operator's manual that includes the installation process will be developed. Finally, a maintenance/system manual detailing the system and its components will be created to support the maintenance of the photovoltaic array.
- Annotated Code
- User's Manual
- System/Maintenance Manual
Testing Requirements
A written test plan will be established to evaluate system performance. Test equipment will be provided by Sedona Energy Labs to test system hardware and software. Test equipment will include the PLC, sensors, actuators, frame, and solar panels. Testing will log sensor input and actuator activity to determine the effectiveness of the system prototype. Testing results will drive the engineering process to a refined product.
- Test plan
- Method of collecting and analyzing results
General Requirements
The system must also adhere to general desirable functions and requirements. A self-calibrating system is extremely desirable, such that the current panel azimuth and elevation can be measured. Simple setup, installation, maintenance, and programming are strongly emphasized due to the client's marketing focus.