HULL DESIGN
The behavior of the canoe during races is greatly affected by the hull design. Because NAU has shown little success using the NCCC’s 2009-2011 standardized hull, the team decided to develop a new hull shape optimized for race performance. The team focused on four design criteria: speed, maneuverability, tracking, and ease of construction.
Since past NAU teams had been restricted to hull shapes imposed by the NCCC rules and regulations, the 2013 NAU team executed extensive research on canoe hull characteristics before executing any design work. Once research was completed, Night Fury’s hull was designed using Prolines©, a boat design and analysis program.
Characteristics the team was most concerned with manipulating were length, beam width, location of beam width, and rocker height.
LENGTH:
A longer boat creates a longer waterline and displaces less water. Therefore, the displacement-length ratio is a good indication of the relative speed of the canoe to other hull designs; the lower the ratio, the faster the canoe.
BEAM WIDTH:
The beam is the widest affects the speed of the canoe as well. The narrower the beam, the less wetted surface area present, creating less drag resistance on the canoe. However, a wider beam provides more stability.
BEAM WIDTH LOCATION:
The location of the beam width affects both the flow of water over the canoe surface (how the water hugs the canoe shape as it passes by) and the canoes ability to turn well when racing. A symetric canoe with the beam centered along the length will be more difficult to turn than one with the beam slightly closer to the stern. For this reason, Night Fury has its beam located towards the stern for the increase in hydrodynamic and turn capacity.
ROCKER HEIGHT:
The rocker determines the maneuverability of the canoe. The more extreme the rocker, the more maneuverable the canoe is, but the less tracking ability available.
By manipulating each of these characteristics individually, the team was able to develop several unique hull shapes. These minor variations of the same basic design determined the best compromise between the design criteria.
To see complete set of design constraints and 2013 NCCC rules VISIT HERE
Canoe Load Modeling
The load modeling for the canoe was done using 3 programs - Prolines©, AutoCAD 2013, and SAP 2000 - in addition to hand calculations which were facilitated with Microsoft Excel.
PROLINES:
Prolines was used to create the desired hull shape for Night Fury based on qualitative features gathered through research. The section shape could be varied, along with the length and curvature of the bow and stern. In addition, Prolines was used to predict the location of the waterline along the canoe and to find the hydraulic load. These calculations were applied later during load case modeling.
AutoCAD 2013:
AutoCAD was a primary tool for both analysis and construction. Used in conjunction with Prolines© software outputs, AutoCAD made models more workable. Then, section properties such as moment of inertia and center of gravity could be determined. In addition, cross-sections were also printed from AutoCAD to be used as a template when cutting plywood during mold construction. Below are some images that show how AutoCAD was used throughout the project.
Various mold views were created in AutoCAD for the final design report to showcase the woodstrip mold and strong back in which the concrete canoe was poured/placed (above, left). The cross-sections were created one by one and used to derive section properties (above, top right). When all the sections were created, a 3D model was completed to showcase the hull shape and center of gravity of the hull along its length.
SAP 2000 and Prolines:
We used Finite Element Analysis to model our canoe
SAP 2000 3D model stress plot
Prolines 2D model moment analysis
Gantt Chart :
This will blow your mind CLICK HERE
Team Hours: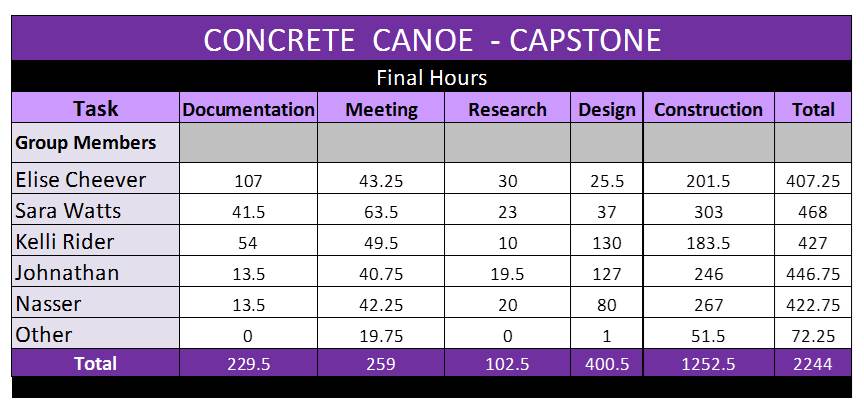