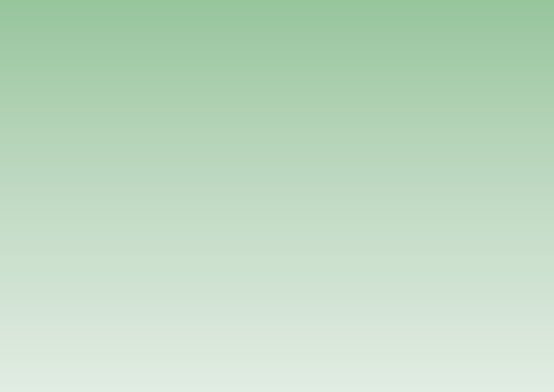
Matthew Roberts,
Alysha Silva, Sanjuana Rico, Kimberly Cook
Department
of Civil and Environmental Engineering, Northern Arizona University



Anaerobic Digestion:
Anaerobic sludge seed from Wildcat
Hill WWTP digested wash water and a manometer measured
gas production
Activated Carbon:
Small-scale filtration system using
activated carbon and plastic bottles



A design
matrix was built to analyze the different treatment options. Each option was
given a value ranging from 1 to 5; 1 being the worst and 5 being the
best. The scores were then added
together.
The
client wishes to upscale the current process to produce biodiesel at a rate of
1000 gallons per week, using approximately 670 gallons of wash water each
week. Based on a balance of system size
and frequency of carbon recharge periods, it was decided to provide a system
that could be used for two weeks before the carbon is spent. M.A.S.K. Engineering utilized Freundlich
isotherm parameters and determined a mass of 20,000 lbs of carbon would be
needed every two weeks to treat the wash water with a factor of safety of
1.36. A system with two parallel carbon
columns, each capable of treating water for two weeks, will be necessary for
maintaining and recharging the carbon.
The reason for having two identical columns is to always have a back-up
in case of a malfunction in the system or delay in carbon recharge.
M.A.S.K.
Engineering considered several treatment options including: activated carbon
filtration, anaerobic digestion, and a packaged wastewater treatment plant
(WWTP).


Mr. Ed Smith
of Flagstaff Renewable Fuels, Ben Moan
at Colorado Plateau Analytical
Laboratory, Larry Lemke at Wildcat Hill
Waste Water Treatment Plant,
Brian Barbaris of the Univ. of AZ, Brandon
Doss of the Chemistry Dept. at NAU, and Drs. Paul Gremillion, Terry
Baxter, Bridget Bero, Charles Schlinger
Wilbert Odem, Joshua Hewes, and Charles Shinham of the Civil and Environmental
Engineering Dept..
Activated
Carbon Treatment Vessel
Activated
Carbon Treatment Vessel
Treated
Water to Biodiesel Wash
Process
Waste Wash Water from Biodiesel Production

•The final
design will be easily scaled and easy to implement.
•The treatment
is effective for the subsequent reuse of wash water.
•A different treatment system might be
more cost effective, but will potentially consume more natural resources which
is beyond the design constraints.
•The current wash process could use the
third wash effluent for the second wash and the second wash effluent for the
first wash.
•A small-scale treatment could be
constructed using recycled materials (except carbon).
•Use a biodiesel production process that
does not involve a water wash.
•Further research on reaction completion
to find the exact concentrations of contaminants in the wash water and
additional research on a mass transfer model to determine the saturation limit
for reuse of the water.

Transesterification
is the conversion of alcohol and triglyceride (UVO) to esters and glycerin in
the presence of a catalyst. Note that the alcohol used, methanol in this case,
must be added in excess to drive the reaction to the right.
Rack of COD testing vials
Using
stoichiometry and assumed levels of reaction completion, concentrations of the
contaminants of concern were developed for the biodiesel mass transfer
analysis. A mass transfer model of
glycerin and methanol diffusing through biodiesel into water was
attempted. A film of water surrounds
the air bubbles rising through the biodiesel where glycerin and methanol
diffuse into the water. These bubbles
break upon reaching the surface and the water droplet then sinks back through
the biodiesel, allowing further mass transfer to occur.
The
analysis that proved the most useful in determining the reusability of the
wash water was the chemical oxygen demand (COD) test because organic molecules
contribute to this oxygen demand. The
contaminants of concern both contribute to COD, but the COD test has no way of
differentiating between the two.
Therefore, the COD test is used to estimate the amount of combined
glycerin and methanol in the water.
M.A.S.K. Engineering relied upon COD testing to trace the contaminants
so regulations on COD discharge were sought after. City of Flagstaff standards were found for
biological oxygen demand (BOD) discharge into sewers. Any facility discharging 1,000mg BOD/L or
more is required to have an industrial discharge permit. Because BOD is always
≤ COD FRF should monitor the COD of their wash water and stay below this
limit for any discharges.


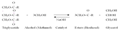


The
Flagstaff Renewable Fuels (FRF) Waste Wash Water Treatment project goal is to
recycle and treat biodiesel wash water to facilitate the expansion of FRF’s
current biodiesel production from a home operation to a 20-30 person
cooperative while minimizing energy and resource consumption. The purpose of
the formation of M.A.S.K. Engineering is to complete the waste wash water
treatment design for FRF. M.A.S.K.
Engineering‘s treatment design will remove the contaminants of concern
(methanol and glycerin) from waste water produced during the Appleseed
biodiesel production process. Several treatment options were identified
including: activated carbon filtration, anaerobic digestion, and a packaged
wastewater treatment plant modeled after municipal treatment systems. The chosen design is activated carbon
filtration because it reduces the contaminant concentrations in an efficient
manner that is easily scaled and easy to implement. This will allow FRF to optimize the use of
water in their biodiesel production process.
Crude Glycerin, Lye & Methanol
Wash Crude Biodiesel with Water
Gravity Separate Water from Biodiesel
Fuel Ready for Blending or Direct
Use
The
Appleseed biodiesel production process involves heating used vegetable oil
(UVO) and adding methanol and flake lye.
Water is used as a solvent to remove undesired by-products such as
soap, glycerin, and excess methanol and lye reactants from the biodiesel. For each gallon of biodiesel produced a
gallon of water is required for washing.
Shown below in red is where the M.A.S.K. Engineering design will be
implemented.
Schematic
of Appleseed Biodiesel Process
Transesterification Equation